Which components may be used in hazardous area’s?
When parts of an area of installation are classified as hazardous areas, it is not always easy to select the appropriate components which may be used in those area’s. In order to understand the selection criteria’s, you must have specific basic knowladge about hazardous areas, substance properties and ignition protection strategies. In this article we explain the main issues and provide guidance for the selection of the appropriate components.
In order to get an explosion safe installation, machinery or work environment, the following basic principle is globally relevant: when your machinery, installation or even single components, are placed within a hazardous area, then this equipment is a potential ignition source for the possible present flammable substances. The basic rule is that such equipment must be prevented from being a potential ignition source. And this prevention of being an ignition source, is done by the manufacturer, by application of special design techniques which are prescribed in specific standards like the IEC 60079 series. By doing so, the manufacturer places its products on the market with a conformity assessment sign. Within the European Economic Area (EEA) the sign is the hexagon Ex sign.
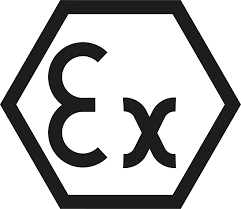
Which hazardous area is applicable?
In order to make the right selection of components, one must understand the diversity of hazardous areas.
A hazardous area is defined as an area in which an explosive atmosphere is present or can be expected to be present, inquantities such that special precautions for the construction, installation and use of equipment
are required (source IEC 60079-10)
An explosive atmosphere is defined as a mixture with air, under atmospheric conditions, of flammable substances in the form of dust, gas or vapour, which, after ignition, permits self-sustaining flame propagation (source IEC 60079-10).
Hazardous areas are, devided into zones (or into Divisions/Classes in some parts like e.g. in Northern America, see out other blog about that).
A zone is defined as an hazardous area classification based on the frequency of the occurrence and duration of the
explosive atmosphere.
In practise there are 3 type of zones for gas/vapor atmospheres and 3 types of zones for dust atmospheres
Gas/Vapor Atmospheres | Dust Atmospheres | Description |
Zone 0 | Zone 20 | area in which an explosive atmosphere (gas/vapor or dust) is present continuously, or for long periods, or frequently |
Zone 1 | Zone 21 | area in which an explosive atmosphere (gas/vapor or dust) is likely to occur occasionally in normal operation |
Zone 2 | Zone 22 | area in which an explosive atmosphere (gas/vapor or dust) is not likely to occur in normal operation, but, if itdoes occur, will exist for a short period only |
So, based on the definitions above, one can conclude that the type of zone stands for the frequency in combination with the duration of an explosievise atmosphere present in a certain area.
The more frequent a hazardous area can be present, the higher the explosion safety requirements of equipment and components in that specific area are!
#1 Selection based on category
The first requirement of equipment, installed, placed or used within hazardous area’s is only to use equipment that is Ex marked. But only Ex-marking is not sufficient. Equipment must comply to the hazardous area where it is used in. The explosion safety requirements of equipment that is e.g. placed in a zone 0 are of a higher standard than equipment used in a zone 2. This can be understand because due to the fact that a hazardous atmosphere in a zone 2 is much less frequent present, than a hazardous atmosphere in a zone 0. So the following general requirements apply to equipment that is suitable for the use in hazardous areas:
Zone | Requirements based on ATEX 114 Directive | Definition | Suitable for use in: |
zone 0 (gas) zone 20 (dust) | Category 1 | Equipment must ensuring a very high level of protection, even in the events of rare incidents, by means of 2 independent protection systems or when 2 fault can occur, independent of each other | zone 0, 1 and 2 (gas) zone 20, 21 and 22 (dust) |
zone 1 (gas) zone 21 (dust) | Category 2 | Equipment must ensuring a high level of protection, even in the events of frequently occuring disturbances or equipment faults, which normally should be taking into account. | zone 1 and 2 (gas) zone 21 and 22 (dust) |
zone 2 (gas) zone 22 (dust) | Category 3 | Equipment must ensuring a suitable level of protection during normal operation. | zone 2 (gas) zone 22 (dust) |
Remark:
Based on the definitions/table above, one may always select a component of a higher grade of protaction as the zone demands. E.g. Equipment of category 1 can be used in zone 0, 1 and 2 (or 20,21 and 22 for dusts repectively).
#2 Selection based on Gasgroup and Dustgroup
Equipment must also be suitable for the gases or dusts that can create a shzardous atmosphere. Gases as well as dusts, are classified based on their ignition properties. For gases there are three gasgroups:
Gasgroup | Examples of gases | Suitable for substances with gasgroup |
IIA | Butane, Ethane, Diesel, Gasoil, Methane etc. | IIA |
IIB | Ethanol, Carbonmonoxide, Hydrogensulfid (H2S) etc. | IIA and IIB |
IIC | Hydrogen, Acetylene, Dichlorodiethylsilane, Watergas (CO+H2), Carbondisulfide (CS2) | IIA, IIB and IIC |
For dusts the following dust groups apply:
Dustgroup | Description | Suitable for substances with dust group |
IIIA | fibers | IIIA |
IIIB | electrical non-conductive dust | IIIA and IIIB |
IIIC | electrical conductive dust | IIIA, IIIB and IIIC |
Remark:
Gas- and dust group IIC and IIIC have higher safety specifications than gas- and dustgroups IIA, IIB and IIIA, IIIB. So equipment that fullfills the requirements of IIC / IIIC can always be used for gases and dusts which require a “lower” gas or dustgroup. The same applies to IIB and IIIB compared to IIA and IIIA.
#3 Selection based on maximum temperature
The last selection criteria for the use of components in hazardous areas, is the temperature class for gases or the maximum surface temperature for dusts. This criteirum specifies the maximum surface temperature of the equipment in a particular zone. The basic rule is that the maximum surface temperature of the equipment must always be lower than the ignition temperature of the flammable substance. See the illustrative figure below.
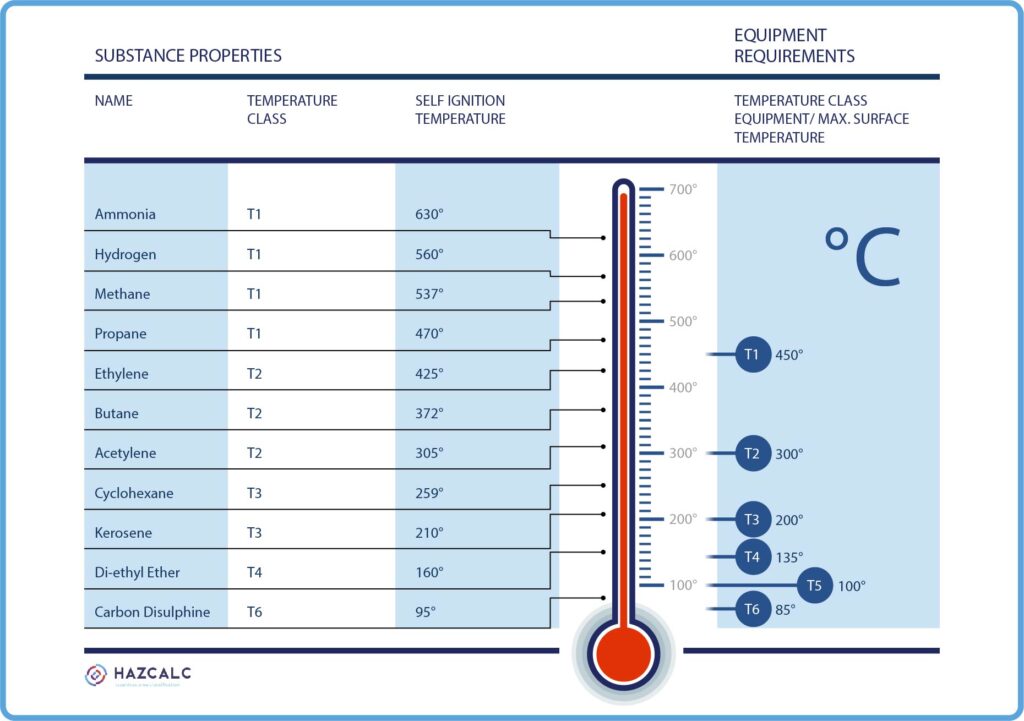
Temperature class for gases
For gases this is expressed by the temperature class and for dusts this is expressed by the ectual maximum temperature.
The following temperature classes are applicable (for gases):
T-class | Maximum Surface Temperature |
T1 | 450°C |
T2 | 300°C |
T3 | 200°C |
T4 | 135°C |
T5 | 100°C |
T6 | 85°C |
So for gases the marking on the equipment shall be a temperature class, e.g. T2. This means that the surface temperature will not be higher than 300°C. The auto-ignition temperature of the substance must be higher than 300°C. So equipment with this temperature class is suitable for hydrogen applications, since hydrogen has a auto ignition temperature of 585°C. The equipment is not suitable for gasoline, since gasoline has a auto-ignition temperature of 247-280°C.
Temperature class for Dusts
The maximum surface temperature for equipment suitable for use in hazardous areas created by dust is always specified with the actual maximum surface temperature, like e.g. T235°C.
One must be ware that a rather high safety marge is applied for dusts, which depends on the minimum ignition temperature (MIT) of a dust cloud and the glow-temperature (Tglow) of a 5 mm dust layer. The following rules apply:
Equipment temperature must be maximum:
Tmax = 2/3*MIT, or
Tmax = Tglow – 75°C,
which is the lowest value.
So for e.g. sugar dust,
MIT = 350°C –> Tmax = 2/3 * 350 = 233°C
Tglow = 430°C –> Tmax = 430 – 75 = 355°C
So, equipment suitable for use in hazardous areas created by sugar dust, the temperature of the equipment must be maximum T233°C.
So whenever selecting equipment, suitable for use in hazardous areas, always select the equipment according to this 1-2-3 selection method.
Of course, beside this basic selection method, other factors can also contribute to the most favorable piece of equipment, like the equipment protection concept. See our other blog-post on ignition protection techniques.